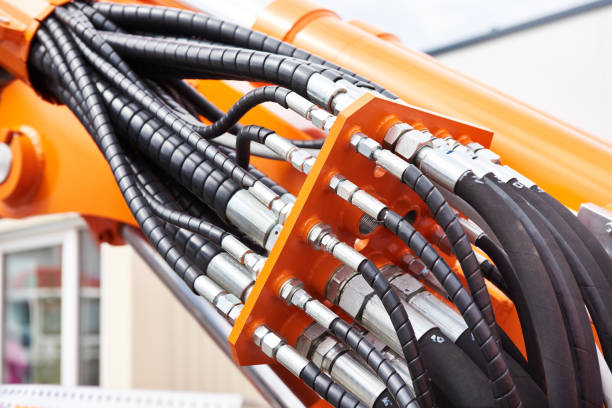
A Comprehensive Guide to Using Industrial Hydraulic Hose
Whether you are a first-time user or an experienced industrial hydraulic hose user, there are several key aspects to consider to get the most out of your hose. These include Materials, Sizing, and Preventive maintenance.
Sizing of Hydraulic Hose
Choosing the right hose for your application is a crucial step in ensuring the performance of your hydraulic system. A wrong inner diameter or length hose can cause many problems, including leaks, inconsistency, and inefficient operation.
To determine the proper hose size, consider the diameter, flow rate, pressure rating, and pressure drop. Typically, a larger inner diameter hose can help you handle a higher flow rate without causing a pressure drop.
In the United States, a Hydraulic Hose is measured in inches. They are usually marked with dashes or a nominal metric equivalent. You can use the dash size to calculate the appropriate inside diameter for your application.
The inside diameter of a hydraulic hose is the best way to determine the correct size. A larger inner diameter allows for an easier flow of hydraulic oil. It also helps prevent friction and restriction. However, a large inside diameter hose could cause routing difficulties and be costly to replace.
The proper hose size will also help prevent hose flow velocity problems. High flow velocities can cause turbulence and friction. In addition, they can cause heat and noise problems. In addition, the correct size will help prevent flow erosion of the hose tube.
Another important aspect of hose size is the cut length. The cut length is measured by subtracting the end of the fitting collar from the fitting collar.
Materials
Choosing the right materials for industrial hydraulic hoses can make a big difference in the performance and lifespan of your system. This is especially true if you use it in a harsh or extreme environment. It is also important to consider the kind of fluid you will be using. Whether water or petroleum-based, the material you choose for your hose will determine its performance.
The inner layer of a hose must be able to handle the kind of fluid you will be using. In addition, it must be able to resist corrosion and chemical impact. You should also check that the compound used in your hose is compatible with your fluid.
The outer layer of a hose is typically made from rubber or synthetic rubber. This outer layer is a protective cover for the inner layer and protects the hose from external factors. It is often oil-resistant and ozone resistant.
The inner tube of a hydraulic hose needs to be flexible. The materials for this part include synthetic rubber, thermoplastics, and fluorocarbons. They can also be made from co-polyester. These materials can be used in a variety of ways.
A hydraulic hose must be flexible enough to stretch across long distances. It must also be able to bend around corners. In addition, it must be able to handle a wide range of temperatures. The material used to make the inner tube will also affect its performance.
Preventive Maintenance
Developing a preventive maintenance plan is important in keeping your hydraulic hoses and equipment running at peak performance. Proper maintenance will reduce the cost of downtime, emergency repairs, and replacement parts. It will also increase the life span of your equipment.
Having a preventive maintenance plan in place will help you identify the components of your hydraulic system that need attention. These include the hoses, fittings, tubing, and special equipment. The benefits of a maintenance plan include reduced downtime, reduced repair costs, reduced parts usage, and maximized economic value.
Maintaining a log of hose and hose assembly conditions is also an important step in preventive maintenance. A log of this information will ensure that the right steps are taken if a component breaks down.
The best preventive maintenance for industrial hydraulic hoses is a surprisingly simple step. It is a visual inspection of the hoses to determine how they are working.
In addition to a visual inspection, a hose system should also be inspected for leaks. Leaks can cause dangerous conditions, and the costs of repairing or replacing them can add up.
In addition to a visual inspection, you should conduct a hose system test at the maximum allowable pressure. This will allow you to identify any leaks that may have gone unnoticed.